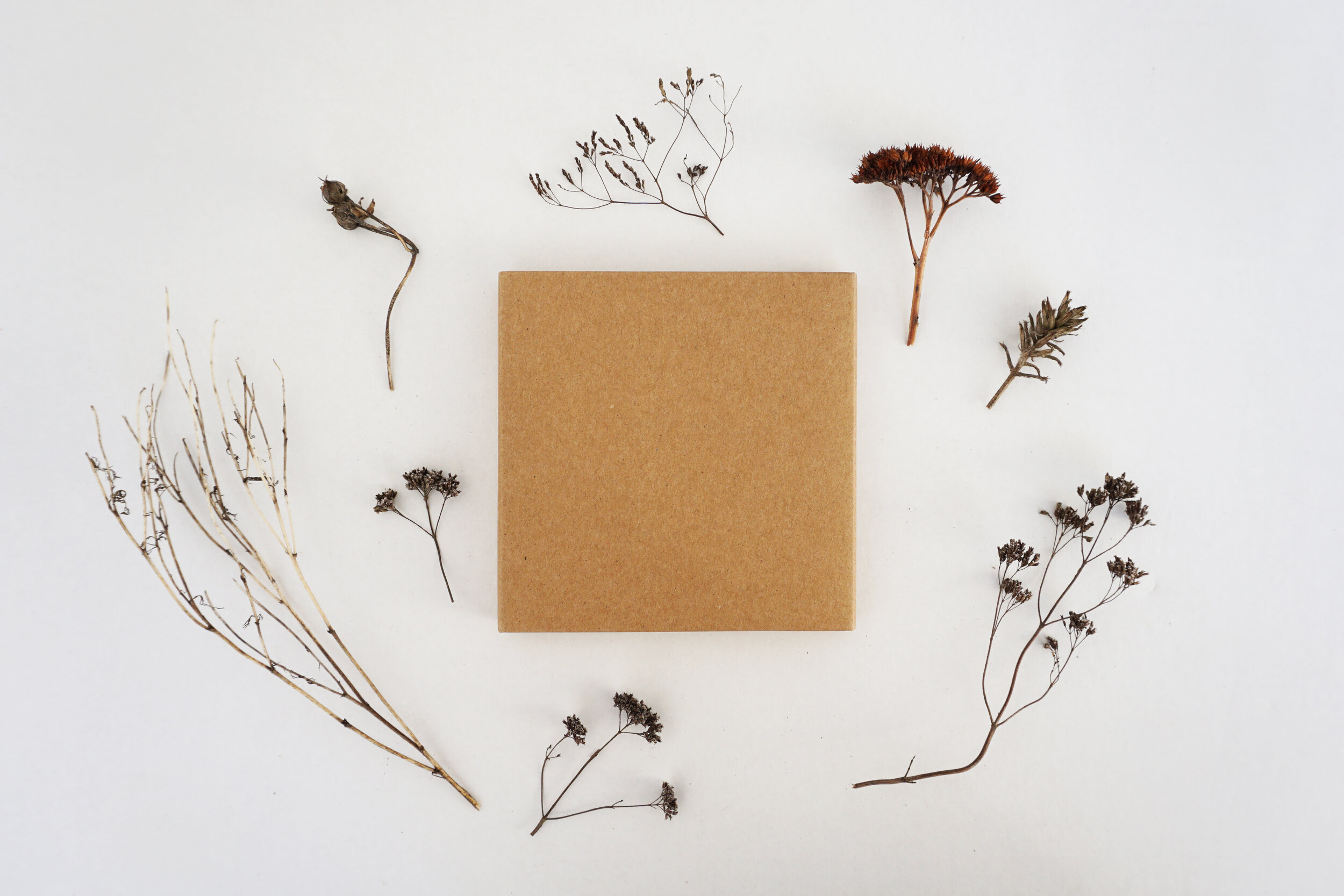
Ecoline
Shoes made 100% with vegetable tanned leather and lining and with sole in Latex/Para soles.
Vegetable tanned leather
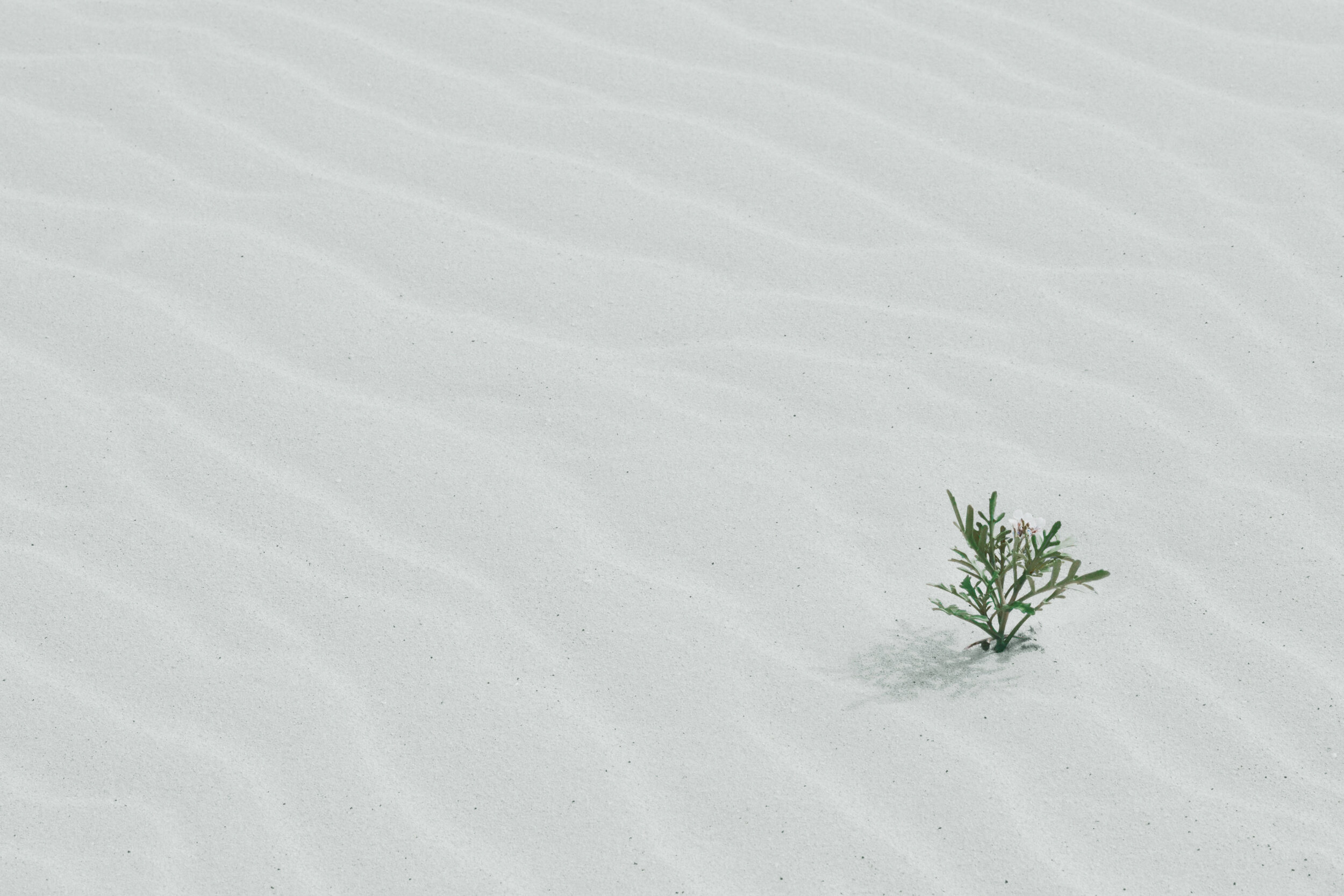
Vegetable tanned leather contains no toxic substances.
Zero waste
No animal is killed for its skin. On the contrary, the raw hides used by our tanneries are the discarded by-products of the food industry producing meat for human consumption.
Water protection
Our tanneries have made huge investments in depuration systems and waste recycling that make them work in full respect of man and the environment.
Sustainable
Being tanned with natural tannins, a vegetable-tanned leather object can be easily disposed of at the end of its life, thanks to its chemical-biological characteristics.
Recycle
Many of the substances used during the tanning process are recovered, recycled and reused in different fields. The wastes are transformed into agricultural fertiliser or reused in the construction field to make bricks.
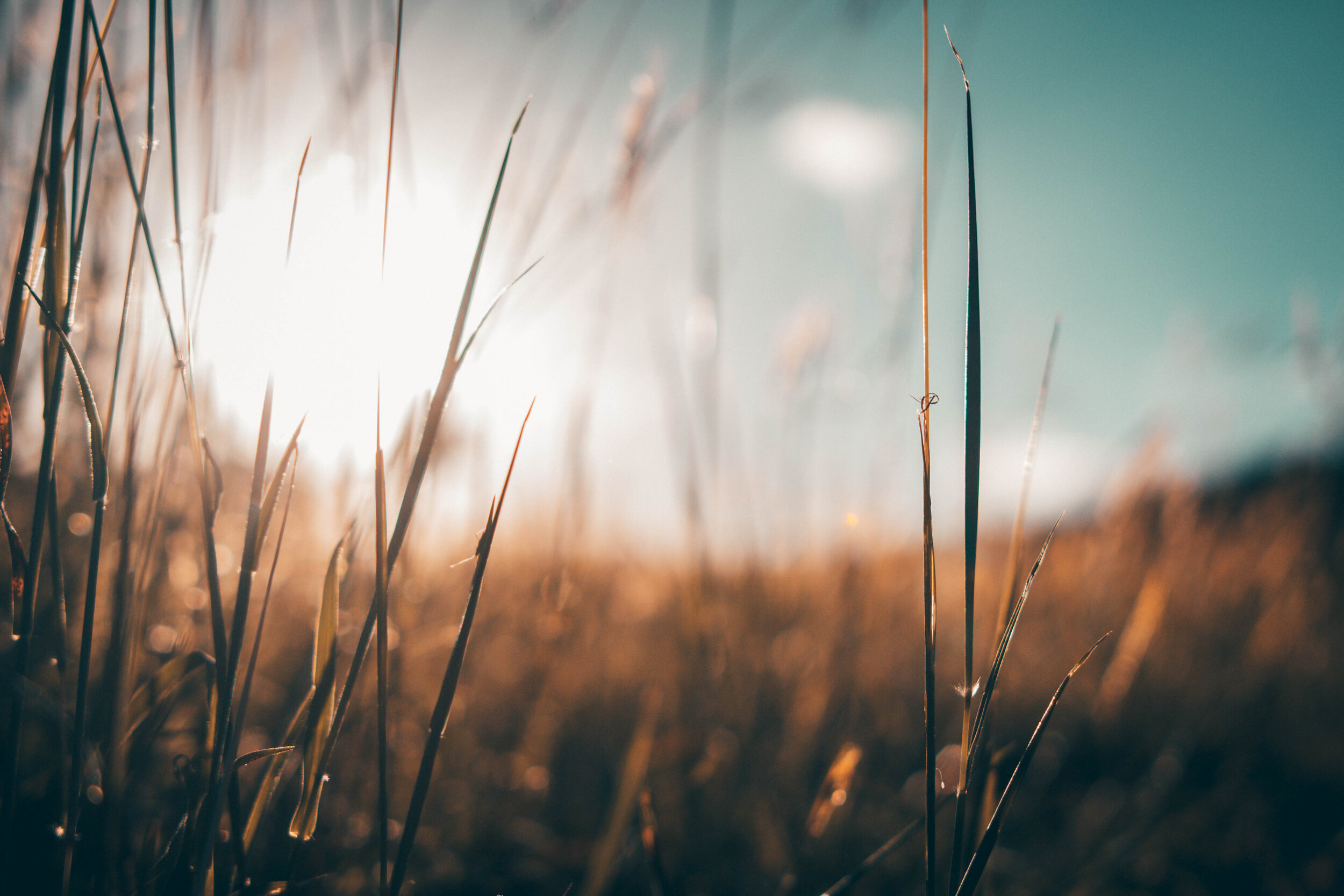
The process of vegetable tanned leather is strictly monitored to ensure low environmental impacts
The sole in Para / Latex
The Para (crepsole) is a natural rubber obtained from the coagulation, and subsequent drying, of the latex produced by the so-called "rubber tree".
The majority of the materials come from South East Asian plantations. It is an ecological product, natural and 100% recyclable, and has a very high elasticity. It has good resistance to abrasion and water, and is unalterable in contact with alkaline, acid and salt solutions; only petrol and solvents can attack it, making it sticky.
It is relatively sensitive to temperatures, showing hardening with cold and softening at temperatures above 40-50 degrees; in any case, bringing the product back to normal temperature, we see a return to its original state with all its characteristics.
Para is an excellent compromise between naturalness and yield. It has many advantages:
It is completely natural and #biodegradable, therefore, it does not present any criticality of disposal.
The scraps produced with the cuts can be reground and recalibrated, to go to regulate themselves in new slabs. It, therefore, limits waste to a minimum, with benefits for costs and the environment.
The manufacturing process is exclusively mechanical and takes place without the use of chemical additives or dyes.